hello
after about 1 year i can say that project is done. automated midi controller for protools DAW HUI protocol. the goal was to get 8 motor faders to control protools and to control faders from protools
for writing and reading DAW mixer automations. the controller contain 31 push buttons 8 solo and 8 mute buttons allso 4 buttons for scrolling 1 or 8 Channels to left or right.
7 buttons for transection panel and 4 buttons for read write touch and latch actions.
all so the controller have 8 OLED screens for channel names DB and solo mute channels symbols.
thats the place to thanks GERRIT and Pual for for the knowledge and the help. i used the slave teensy code of gerrit zeus midi controller project as a reference, and i modified it for my needs.
for this project i write custom pcb for easy and safety connections and for easy parts replacements.
the project contain:
2X teensy 3.6
2X Multiplexer 16
1X TCA9548A Multiplexer
4X l9110s Dual Hbrige
8X OLED screens 128X64
31X silicon push buttons.
2X DC TO DC stepdown
1X 12v 4A PSU
enclosure and panel is a custom made by me
i still have some minor bugs like: when i scroll 8 faders right i get solo symbol in the first channel screen. thats behavior related to the hui protocol data action and my code. still trying to fix it but allso i can live with it for now.
the second issue is some problem of buffering screen to get realy fast response on screen with out delay the system for fast faders action.
i used u8g2 lib for my screens but the best i could get from all of my experiments is half top screen to get work with fast fader response . any other full buffer u8g2 constructor i used cuse my system delay in action and looks like overflowing.
all so in this case i can live with it by putting all parameters on top of the screen to see them all.
from my discussions with olikraus the U8g2 lib writer on this issue the problem its about overflowing the ram. im still looking for a ways to solve it .
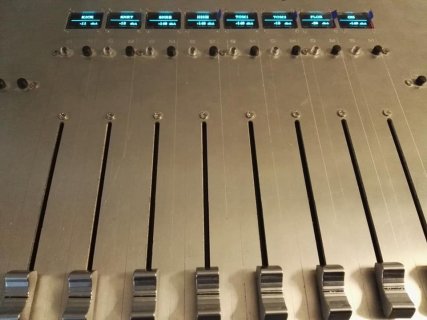
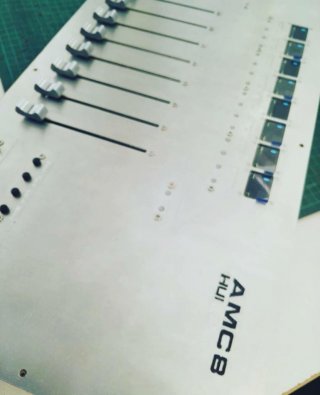
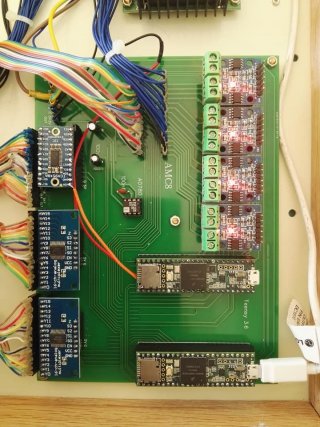
Rota
after about 1 year i can say that project is done. automated midi controller for protools DAW HUI protocol. the goal was to get 8 motor faders to control protools and to control faders from protools
for writing and reading DAW mixer automations. the controller contain 31 push buttons 8 solo and 8 mute buttons allso 4 buttons for scrolling 1 or 8 Channels to left or right.
7 buttons for transection panel and 4 buttons for read write touch and latch actions.
all so the controller have 8 OLED screens for channel names DB and solo mute channels symbols.
thats the place to thanks GERRIT and Pual for for the knowledge and the help. i used the slave teensy code of gerrit zeus midi controller project as a reference, and i modified it for my needs.
for this project i write custom pcb for easy and safety connections and for easy parts replacements.
the project contain:
2X teensy 3.6
2X Multiplexer 16
1X TCA9548A Multiplexer
4X l9110s Dual Hbrige
8X OLED screens 128X64
31X silicon push buttons.
2X DC TO DC stepdown
1X 12v 4A PSU
enclosure and panel is a custom made by me
i still have some minor bugs like: when i scroll 8 faders right i get solo symbol in the first channel screen. thats behavior related to the hui protocol data action and my code. still trying to fix it but allso i can live with it for now.
the second issue is some problem of buffering screen to get realy fast response on screen with out delay the system for fast faders action.
i used u8g2 lib for my screens but the best i could get from all of my experiments is half top screen to get work with fast fader response . any other full buffer u8g2 constructor i used cuse my system delay in action and looks like overflowing.
all so in this case i can live with it by putting all parameters on top of the screen to see them all.
from my discussions with olikraus the U8g2 lib writer on this issue the problem its about overflowing the ram. im still looking for a ways to solve it .
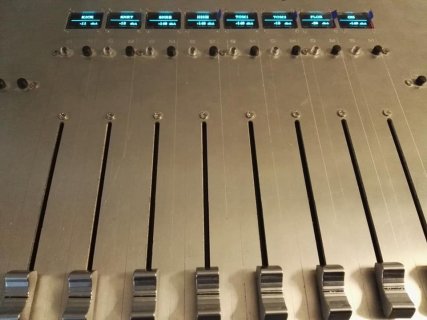
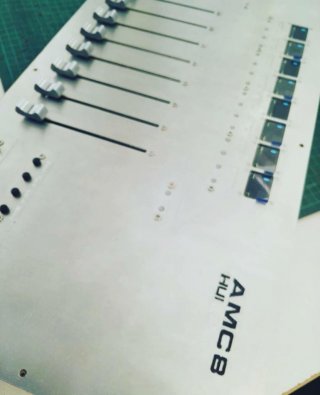
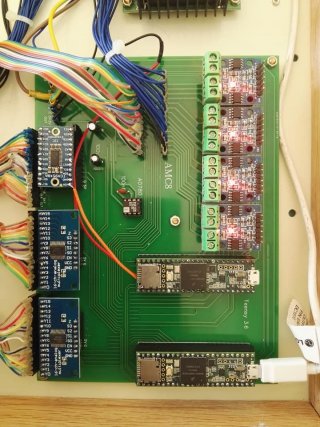
Rota
Last edited: